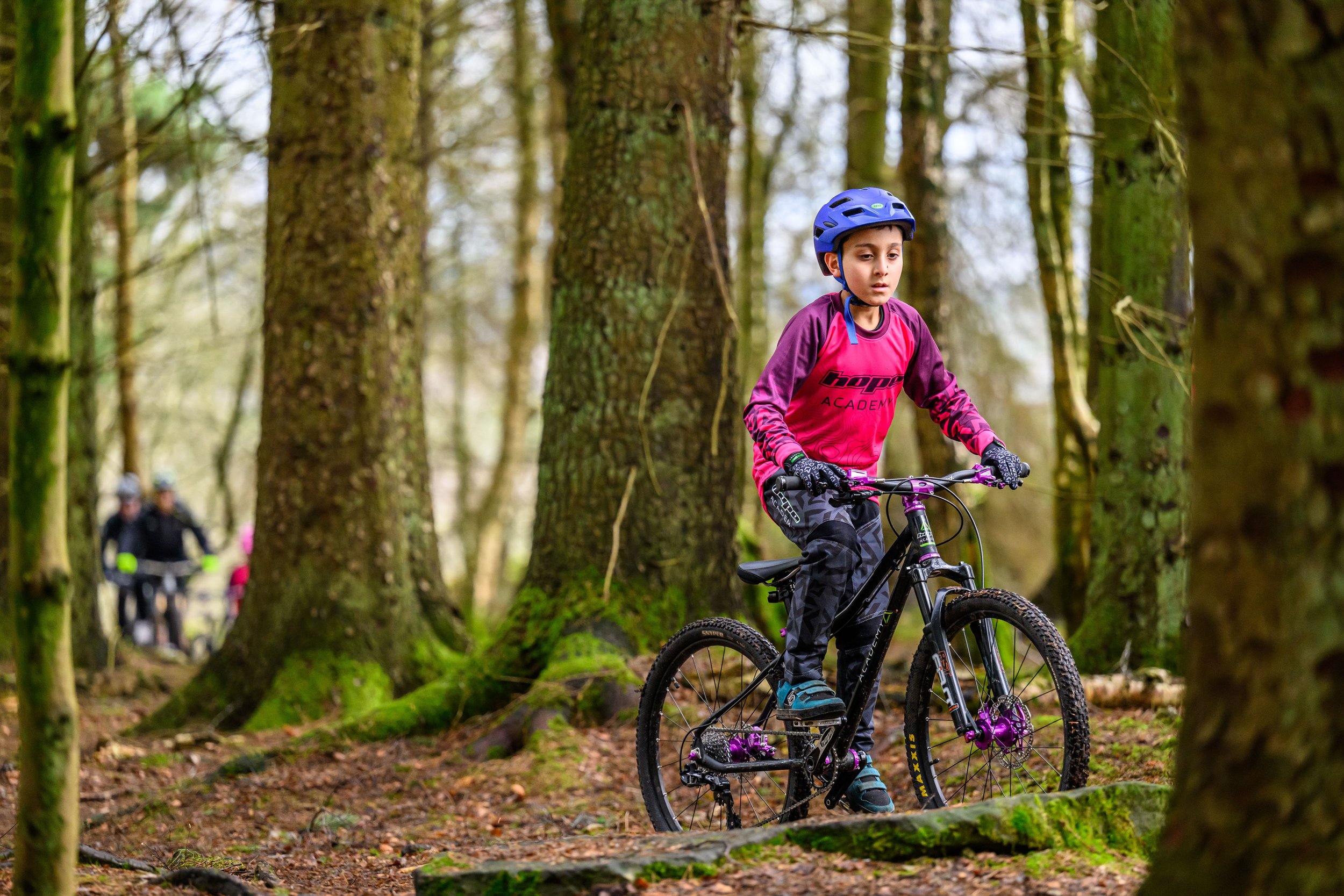
OUR SUSTAINABILITY PROMISE
Hope Academy follows the model of a circular economy, a system that focusses on recycling and reusing as much as possible. The longer we keep our Academy bikes in use, giving life to a bike again and again, the more we can reduce our dependence on new materials and curb overall demand.
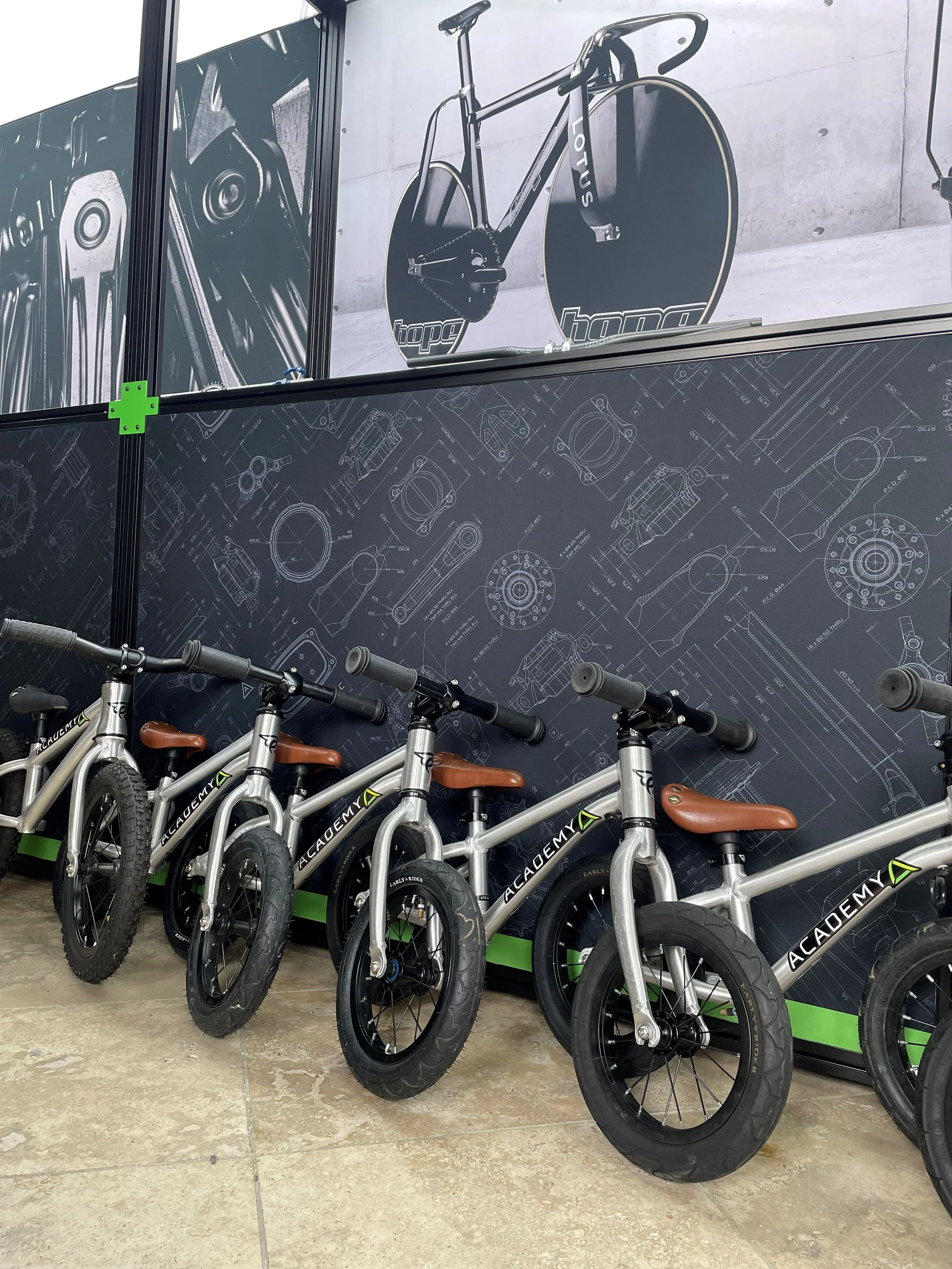

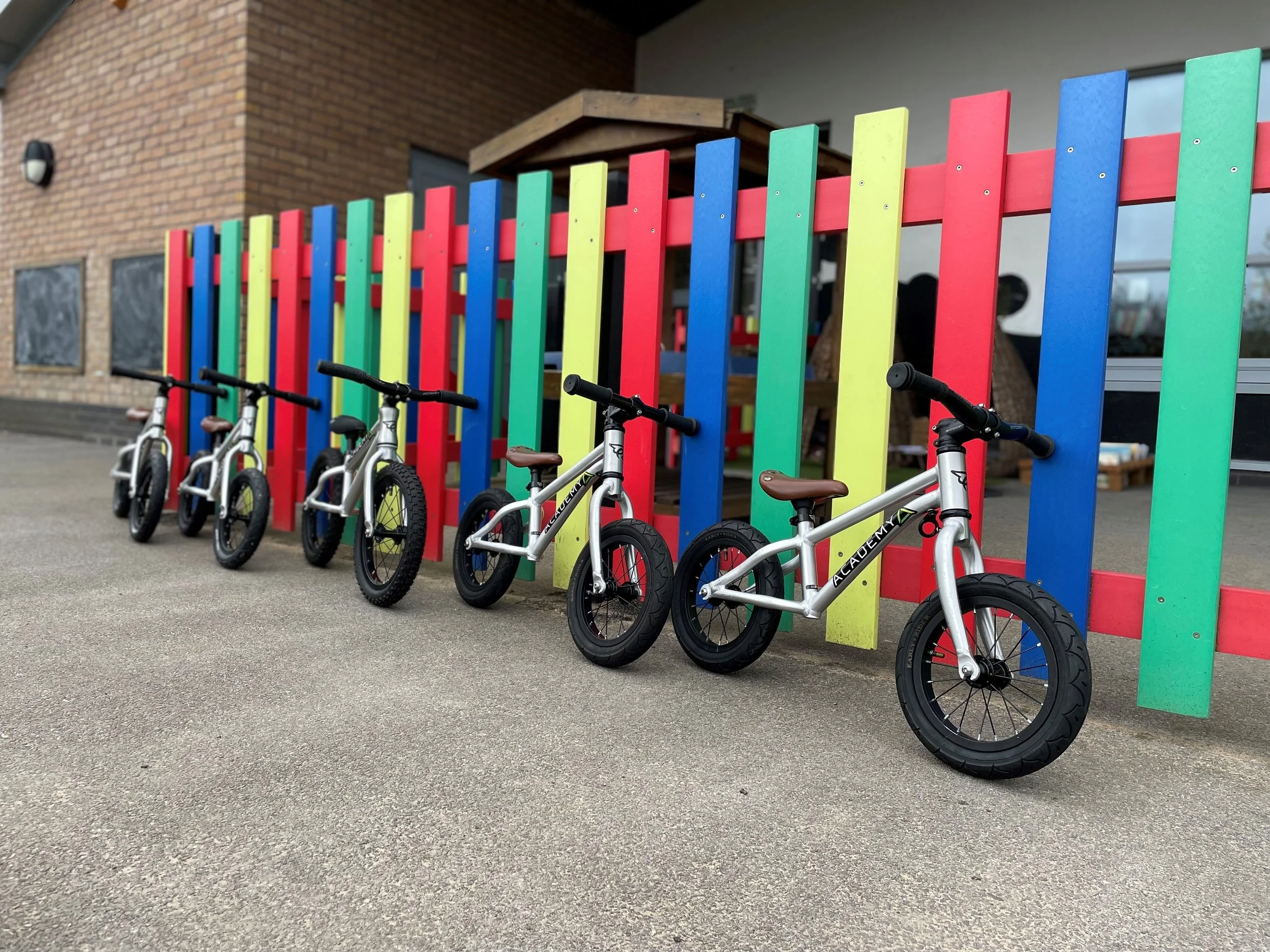
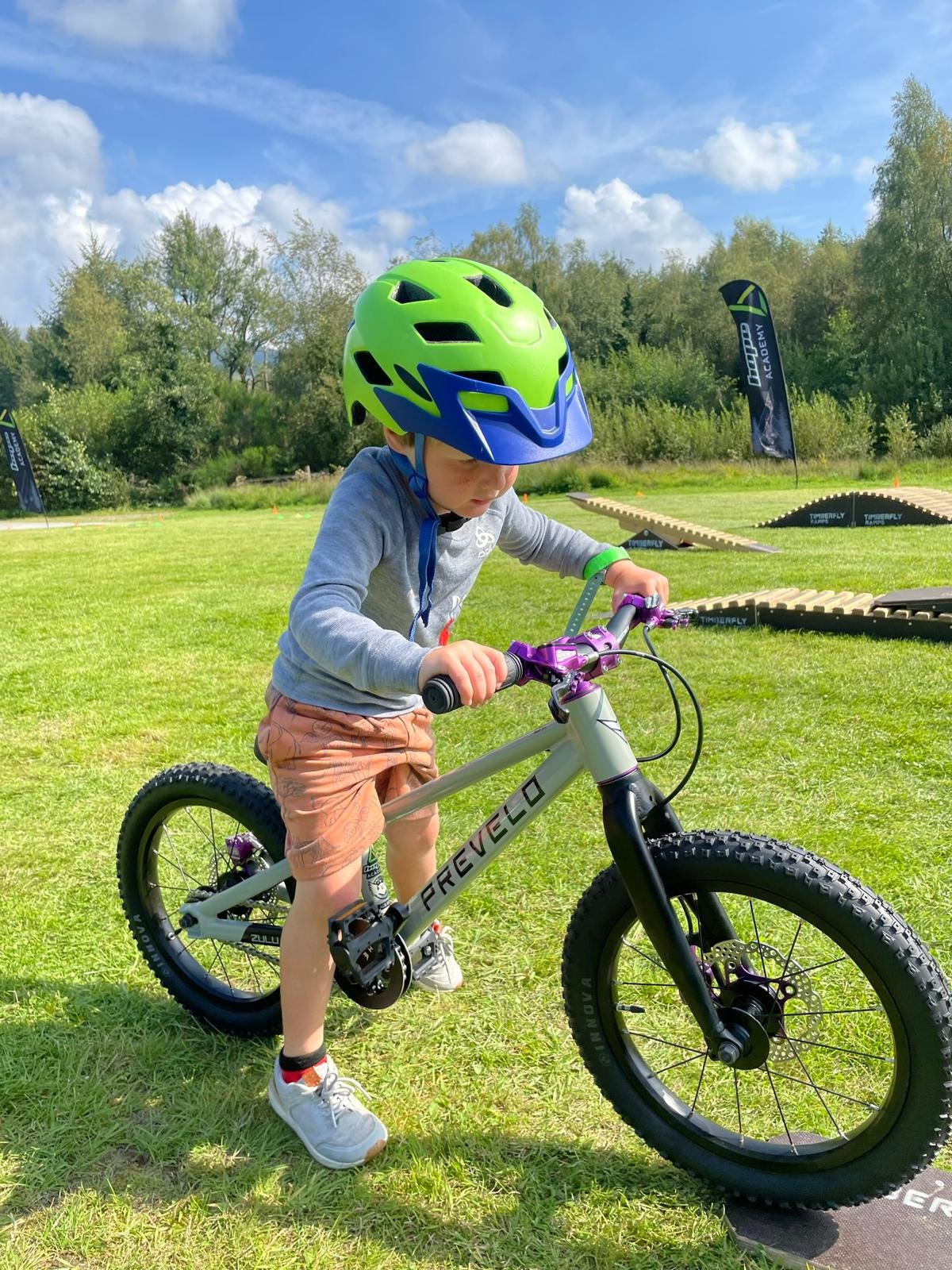
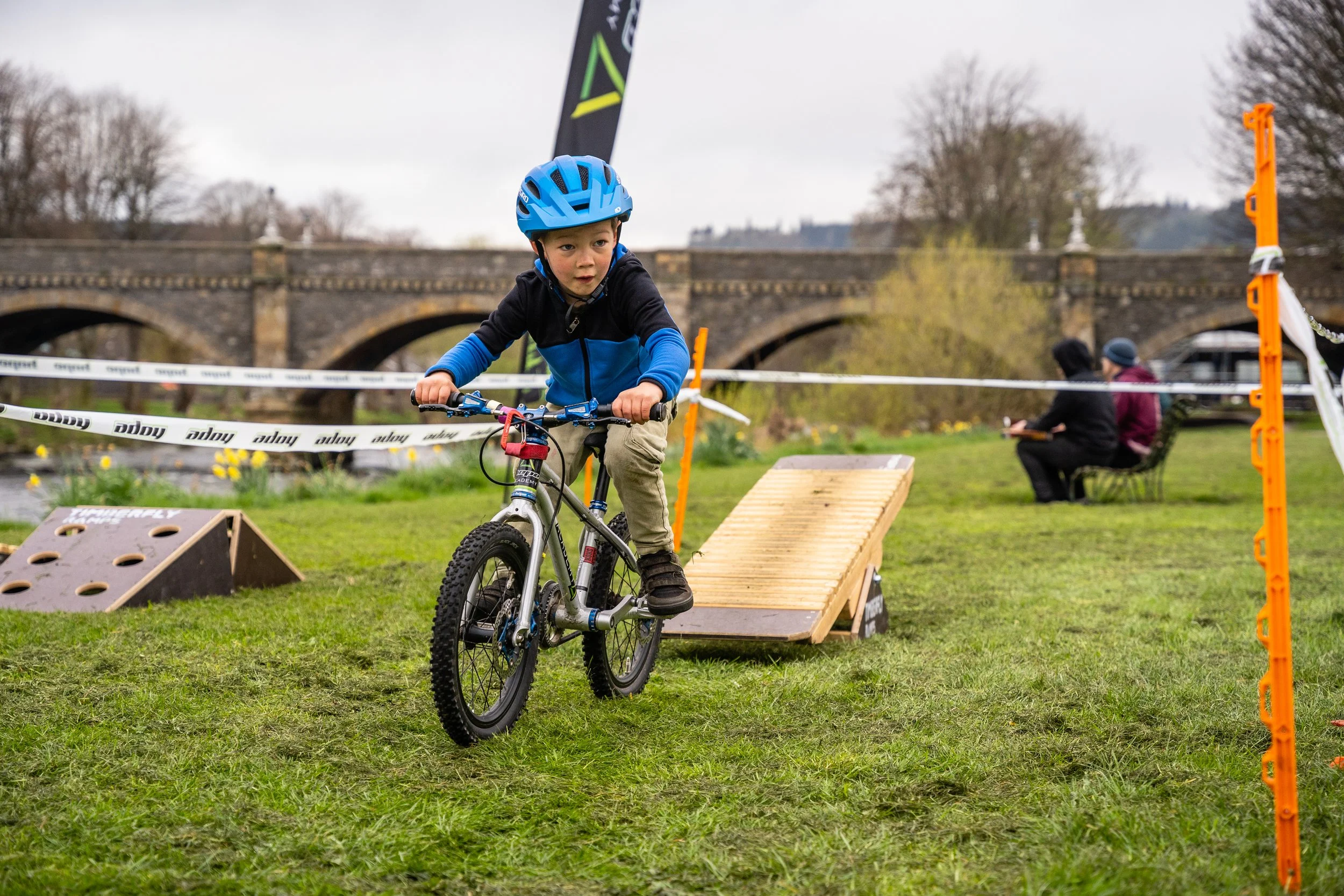
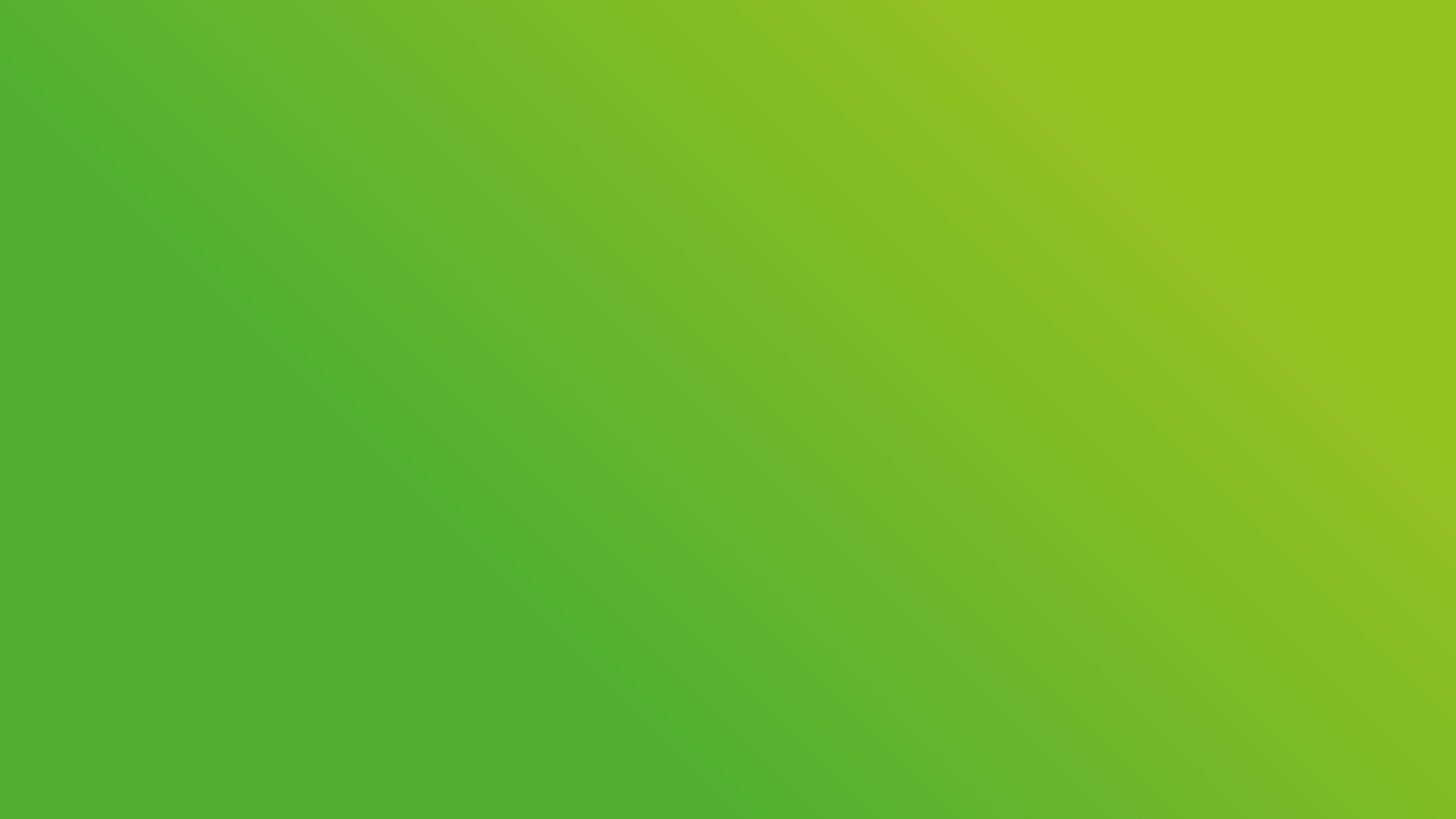
We have chosen to partner with some of the best brands in the industry. These brands have been carefully selected for their high quality bikes, enabling us to keep our bikes in the scheme for as long as possible. We still have bikes from our very first fleet in 2017 in the scheme today.
We replace any standard components with our own, which are manufactured, designed and tested on-site in Barnoldswick, and donate all the standard parts that are removed to local bike charities to make sure they don’t go to waste.
When you upgrade your bike, your old bike is returned to us in the new bike’s box. We re-use the same boxes for deliveries and returns until it’s no longer practical, at which point they are recycled.
Our packaging supplier has been awarded ISO 14001 accreditation, as their packaging is manufactured with at least 90 per cent recycled fibres, and any new material comes from certified sustainable softwood forests. One hundred percent of our waste paper and cardboard is recycled.
All bikes returned to us are fully serviced and repaired before being sent to their new families. We use frame protection to keep our bikes looking great for as long possible.
After all the adventures and the tracks and trails our bikes see with their families they can become a little tired and eventually there comes a time when we need to take them out of the scheme, but fear not! Our bikes don’t end up in landfill. They are all fully serviced and donated to local schools and women’s refuge centres, where they will spend their retirement doing what they do best: helping young children have fun on two wheels.
Virtually everything we do at Hope HQ is developed, prototyped, machined, anodised and assembled on-site, meaning our products save on transport miles.
One hundred percent of our metallic waste is recycled, meaning all swarf, leftover metal and mistakes are sent off to be recycled. Not only does this make financial sense, it is also good for the environment.
We also have a filter system for our machine coolant that enables us to continually recycle the liquid.